Is Modular Construction Right for the Next Project?
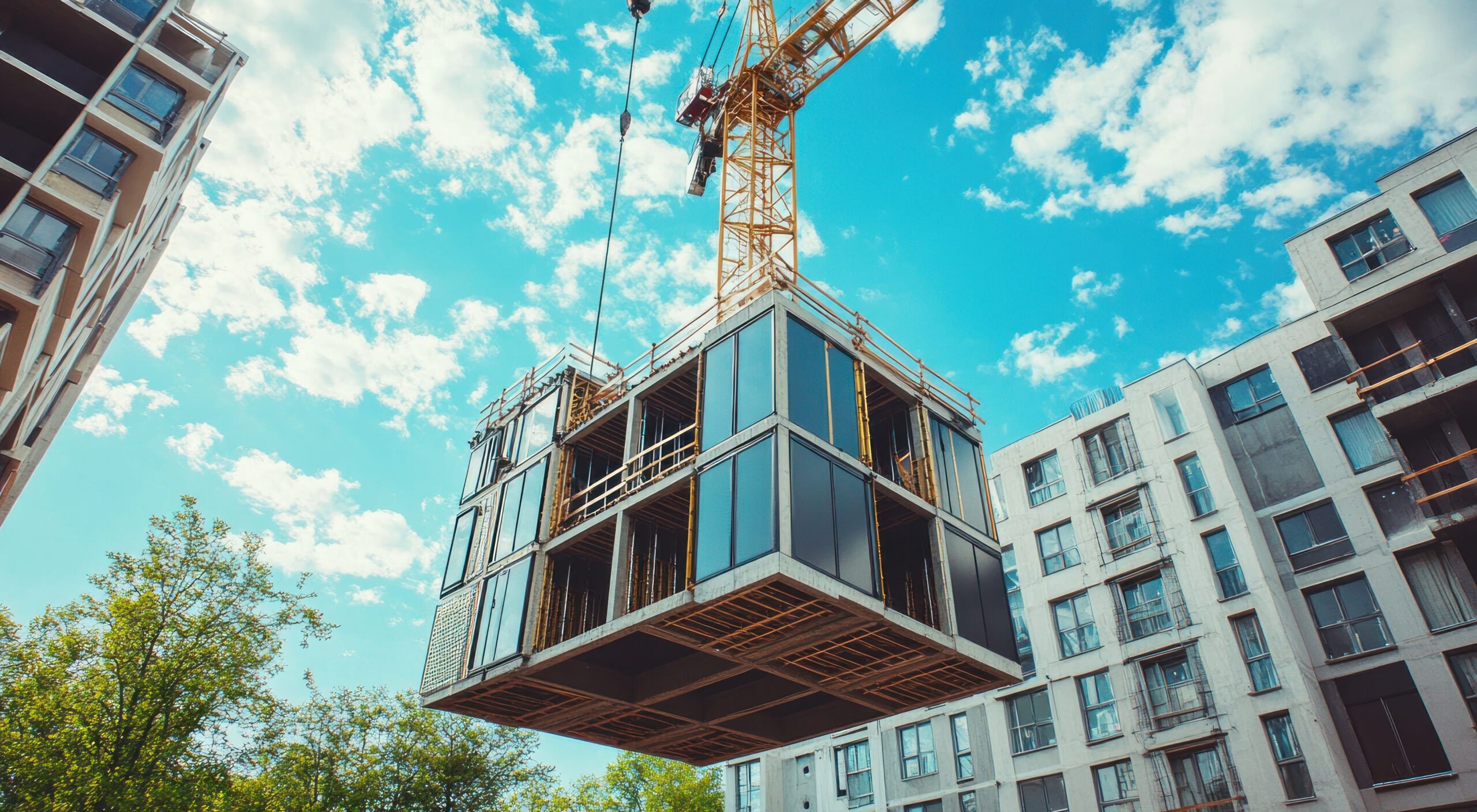
Though prefabricated (prefab) and modular construction has existed for decades, its adoption has accelerated in recent years due to shifts in market demands and advancements in technology that have replaced outdated perceptions of such structures with a host of significant advantages.
This construction method involves assembling sections or modules of a building off-site in a controlled environment before transporting and installing them at the final location. On-site construction and its prefab and modular alternatives each offer distinct upsides and present potential challenges. Here are the basics that can help determine whether this construction method is a viable and attractive method to achieve certain goals.
Key Elements of Successful Prefab and Modular Construction Projects
- Standardization with customization: While prefab emphasizes established and standardized designs, advancements in technology now facilitate a certain degree of customization.
- Variety of materials: Prefab can involve structures built of steel, wood, concrete, and other materials. This allows for flexibility depending on the project’s requirements and structural integrity needs and facilitates material selection based on changing market conditions caused by supply chain disruptions, tariffs, and other factors.
- Leveraging technology: Building Information Monitoring (BIM) allows all project stakeholders to visualize a structure in its entirety, facilitating collaboration between architects, engineers, owners, and construction teams and allowing for early identification and resolution of potential issues or problems.
- Versatility: Prefab and modular construction is well-suited to a wide range of buildings and facilities, including manufactured homes, tiny houses, modular townhouses, fast-food restaurants and retail outlets, health care and educational facilities, warehouses and data centers, and temporary or emergency housing. Modular construction also allows for easy expansion or relocation of structures.
- Sustainability: Prefab is inherently more resource-efficient, as factory-based production minimizes material waste. The precision of manufacturing processes ensures that components fit together seamlessly, reducing errors and the need for rework. The environmental benefits also extend to lower energy consumption during assembly and transportation, making this method a preferred choice for developers striving to meet green building standards.
Why Prefab and Modular Construction May Be the Better Call
Embarking on a prefab or modular construction project offers several advantages over traditional builds, including:
- Speed: Since construction occurs simultaneously in the factory and on-site, project timelines may be significantly reduced, making this method ideal for time-sensitive projects.
- Cost and efficiency: Prefab reduces labor costs, reduces material waste, and enhances overall project predictability, including minimizing weather-related delays. Prefab streamlines production in a factory setting, where conditions are controlled and efficiency is maximized. For instance, modular units can be built simultaneously with site preparation, which may reduce project timelines and allow developers to deliver projects faster, without compromising quality.
- Improved quality control: A factory setting for much of the prefab building lifecycle could provide more consistent monitoring, advanced machinery, and standardized processes that reduce the likelihood of defects and inconsistencies.
Why a Different Call Might Be Made
Prefab and modular construction, being far less established than on-site builds, comes with several significant implementation challenges:
- Higher upfront costs: Factories require specialized equipment, skilled labor, and logistical planning, making initial capital expenditure higher than traditional construction methods.
- Transportation and logistics Issues: Transporting large prefab components to the construction site poses logistical challenges, including potential damage during transit and limited access to restrictive urban sites.
- Market acceptance: “Cheap,” “flimsy,” “temporary” – these perceptions are still held by the public, despite significant advancements in quality and viability. Some owners and contractors harbor doubts regarding the aesthetic and architectural flexibility of modular designs.
- Compliance: Since prefab components are manufactured off-site, they may be required to meet the regulations, building codes, and permitting requirements of both the production location and the final building site, adding a layer of compliance complexity.
- Contractual concerns: Prefab construction involves multiple parties, including manufacturers, transporters, and on-site contractors. Clear contractual agreements that may differ substantially from AIA (American Institute of Architects) and other standardized contracts are essential to define responsibilities, timelines, and risk allocation.
The future looks promising for prefab and modular construction. As the construction industry continues to adapt to global challenges such as urbanization, labor shortages, and potential tariffs, these innovative methods are poised to play a pivotal role in shaping the built environment. The bottom line is that prefab and modular construction represent a forward-thinking, alternate approach that combines efficiency, sustainability, and technological innovation.
In This Article
You May Also Like
ICE Raids on Construction Projects: Best Practices for Mitigation OSHA Update: Construction Employers Now Required to Provide Properly Fitting PPE